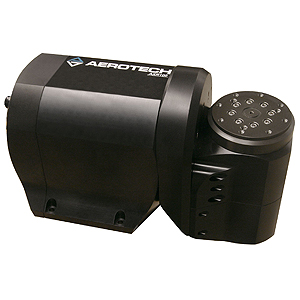
Aerotech introduces its new AXR series 2-axis rotary micropositioning assemblies combine yaw and tilt axes that enable high speed and high throughput micromachining of complex 3D structures such as MEMS components. As part of the enabling technology for many microfabrication techniques, the rotary assembly provides an accurate platform for positioning and manipulation from a precision aligned hemispherical surface.
With two standard module sizes offering nominal system loads of 15 kg or 30 kg, the AXR includes a direct-drive yaw (B) axis capable of unlimited rotation up to 1000 rpm with a sub arc-sec position resolution. The second tilt (A) axis offers a fixed rotation over -10 to +100 degrees and is available with brushless servomotor direct-drive for high speed positioning to 720 degrees/sec, or for the larger sized version as a servomotor driven geared option with an anti-backlash harmonic gearbox that offers a much higher continuous torque that will suit heavier load applications where lower speed operation and reduced overall accuracy is tolerable.
As with all of Aerotech's precision mechanics, a choice of calibrated and un-calibrated versions is available to match specification, ensuring competitive and economical system costs. Throughout the range, high line count optical encoders offer angular resolution to 0.04 arc-sec and with multiplier and advanced amplifier technologies, help to ensure smooth motion and excellent position stability for exacting micromachining. With HALAR calibration, the all direct-drive version of the AXR can provide a +/- 3 arc-sec positional accuracy whilst the geared version has a +/- 5 arc-sec accuracy. Bi directional repeatability across the direct-drive versions is +/- 1 arc sec, compared with geared versions' +/- 5 arc-sec. Un-calibrated specifications for accuracy are +/- 30 arc sec for direct-drive version with +/- 50 arc-sec for the geared version.
The AXR series features an integral pneumatic rotary union for vacuum or air-activated work holding and the ready to run assembly includes motor and feedback cables and connectors. Both module sizes may be ordered in a choice of configurations where the yaw axis tabletop is either at the centre of rotation of the tilt axis, or offset at 100 mm below the centre of rotation for the smaller assembly or 125 mm for the larger version. The orthogonal mounting accuracy is within 10 arc sec.
All configurations can benefit from an additional sealing option for increased protection against dust and dirt. Further options include a counterweight attachment to help balance offset loads, a manual 3-Jaw chuck for the yaw axis for workpiece clamping, and a pneumatic locking brake fitted to the tilt axis that limits stage motion during micromachining. The durable black anodised aluminium construction includes a yaw axis tabletop with a matrix of M5 Helicoil inserts for convenient customer fixture interfacing. Heavy duty, high precision bearing sets help to guarantee a low maintenance/long working life which is specified at 20,000 hours MTBF for the non-contacting direct-drive version and 15,000 hours for the geared version.
The AXR series was developed as part of Aerotech's laser and medical industry solutions. This includes a wide range of micropositioning mechanics that combine with advanced motion controls to help produce complex components at fast production throughput rates with no-compromise on quality and accuracy. The AXR joins linear/rotary axis configuration designs such as the LaserTurn and Vasculathe that offer bespoke solutions for medical stent manufacture and other cylindrical geometry components.
The new AXR series 2-axis rotary micro positioning assembly is typically supplied as a part of a complete motion control sub-system with Aerotech's advanced motion controls and servo amplifiers. HALAR calibrated versions include an error compensation lookup chart which is stored within the controller to ensure optimum accuracy performance. Aerotech's motion controls include the PC based A3200 Digital Automation Platform , the new MotionPAC programmable automation controller, and the Ensemble and Soloist stand-alone motion controllers. Through the range PC-based software-only control or standalone solutions are available in rack or desk mounted options. Aerotech's wide choice of machine controls and sophisticated motion commands include IEC61131-3, Microsoft .NET Framework and LabVIEW programming capability with advanced software and analytical functions that are designed to optimise machine performance, increase precision and improve throughput.
|